Challenges and Solutions
The clutch-brake system has three main parts: the body connected to machine shaft, the clutch friction disc and the brake friction disc. Currently the wear check is done manually by qualified technical staff, stopping the machine, with all involved downtime cost. Furthermore in case of bad
conditions running it is uncontrolled.
Within the Smarter-SI project a new smart sensor will be developed, intrinsically integrated in the clutch-brake, because external indirect sensors give poor results.
The main advantages are:
- Monitor wear of pads and measure maximum temperature at friction point ensuring self-monitoring capability, which is a key solution in big machinery
- Sensor integration in a wheel ensuring direct measurement
- Energy harvesting, Wireless data transfer and Low power electronics
The manufacturing is considered feasible as there are no critical designs or processes in the final foreseen solution.
SMARTER-SI Support
The project partners of SMARTER-SI can provide all necessary technologies and building blocks to realise this innovative sensor system with the desired TRL: An energy harvester (building block by Hahn-Schickard), sensors and signal conditioning (building block by IK4-Ikerlan), electronics (building block by IK4-Ikerlan) and wireless emission (building block by Hahn-Schickard).
The SME Goizper contributes in the integration of sensors and energy harvesting into pilot clutchbrake system and also testing the smart system in industrial like environment.
Impact/What’s next
Goizper expects to check the system, firstly in a test bench and later on in field applications, between 5 and 25 units, during 2017, and after that, assuming that the results are promising, optimise it and launch it to the market. It is estimated that this monitoring capability will increase the revenue of Goizper by 1M€ over the next 5 years from the ending of the industrialisation phase.
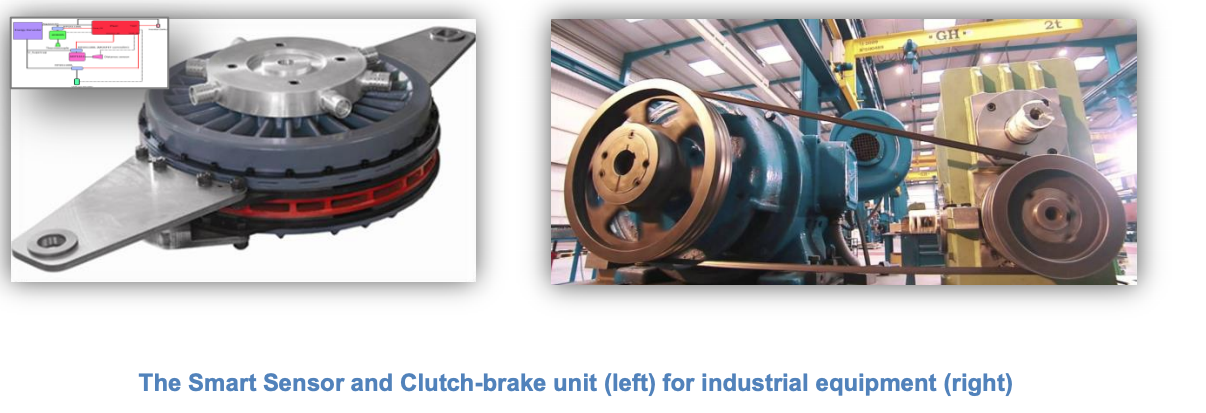