Challenges and Solutions
For reasons of continuing monitoring, higher quality and energy saving Industry 4.0 offer new markets field of process industry and renewable energy sector on highest degree suitable for SMEs (number of pieces 10T- 100T). Pressure sensors for example must be very close to the process
(instead of by-pass) and high performance parameters including long term stability must be guarantee under higher temperature, harsh environment and wider range of pressure. More-thanMoore technology are essential necessary for the realization but the development of own technologies is not payable for an SME and would need too much time.
The solution for such required pressure sensors lies in a holistic analysis of the different signal components and the integration of the best available building blocks. The lower sensitivity of conventional thin film constructions was compensated by the building blocks of a piezoresistive
silicon strain gauge, realized by RTO CiS and metallization and passiviation, realized by TNI, CiS and SME. The strain gauge measures the mechanical stress under load of the membrane and is directly in
contact with the medium, measured.
SMARTER-SI Support
Based on the excellent market knowledge of the SMEs for high performance pressure sensors the DIH Smarter-SI developed and manufactured an efficient solution by using advanced technology platforms and building blocks available with a high TRL in the research consortium. Under the criterion of a fast access to market the DIH elaborated a fast Proof-of-Concept for first market evaluations and a transparent system concept regarding further miniaturization, cost reduction, technological compatibility at the interfaces of the building blocks including the transfer to industrial processes for mass production.
Digital Skills
The contribution required for the solution have been:
Sensor system consist of building blocks like steel or LTCC spring membrane (provided by SMEs), high sensitive and ambient resistant transducer (provided by CiS), back side wafer preparation at the interface to membrane (provided by CiS), high temperature resistant metallization (provided by TNI) and passivation layer (provided by TNI).
Impact/What’s next
Both SMEs ADZ and PMST need innovative products to survive in the global competition, increase their market share and open up new application fields, such as the process industry, transport and renewable energies (hydrogen).
The sales forecasts of the two SMEs are promising, for ADZ: in 2018 50T€, in 2019 100T€, in 2020 200T€, and for PMST: in 2018 50T€, in 2019 150T€, in 2020 250T€.
Inexpensive ceramic differential pressure transmitters with a smaller size and higher accuracy make it possible for SMEs to address the needs of the market for sensors with high precision and application under harsh environmental conditions.
The achieved results and the further potential for miniaturization, reliability and robustness create outstanding opportunities for the SMEs involved in acquiring new customers and orders. For example, such sensors can be used for pressure ranges up to 8000 bar, which was currently only
possible with sensors made of steel or ceramic.
A good double-sided protection of the sensitive bending plate, realized by validated components from research, opens the market for the next generation of differential pressure sensors.
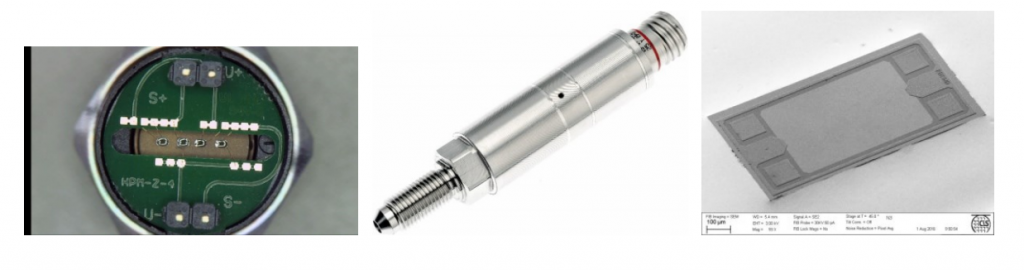